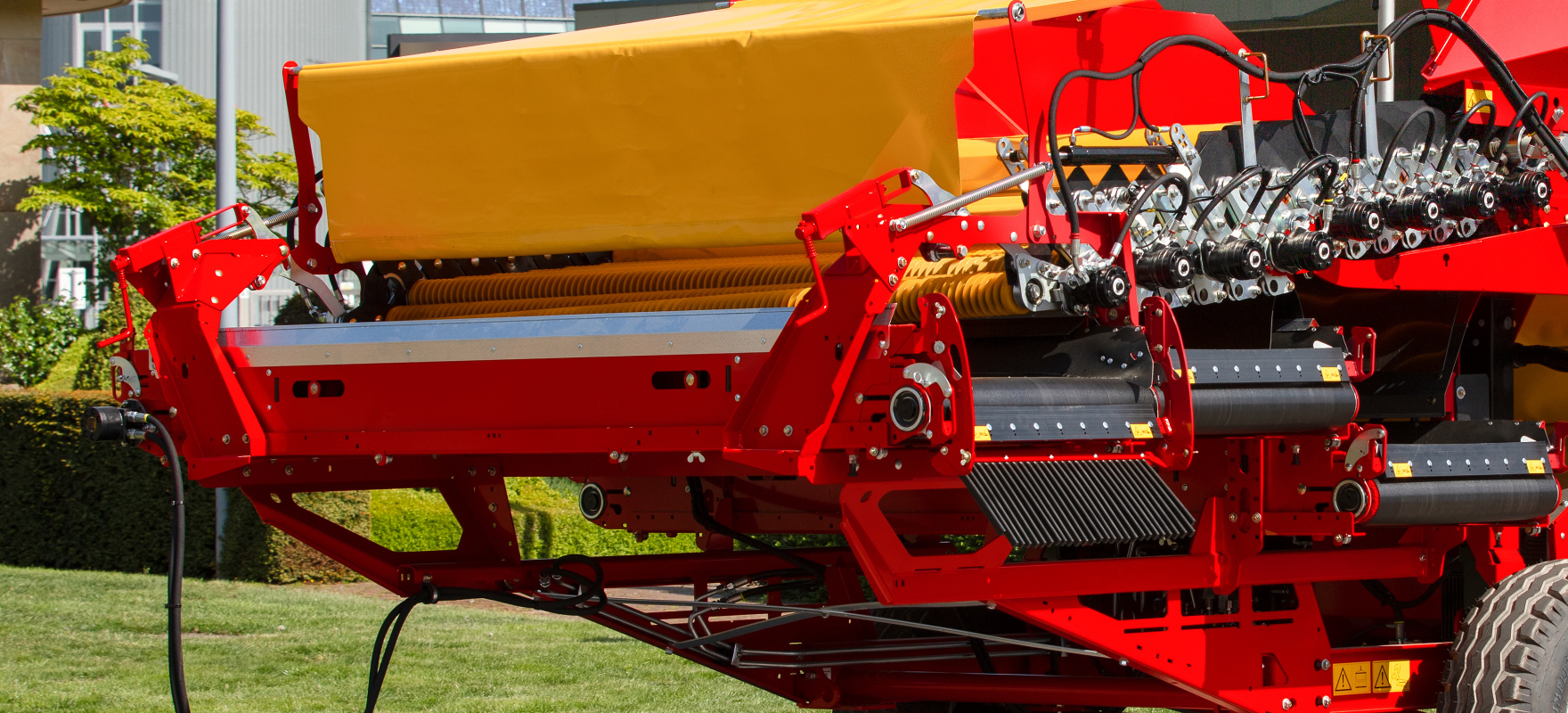
RH series
RECEIVING HOPPER WITH OPTIMISED INTAKE AND INCREASED OUTPUT
For the 2020 season, the RH-receiving hoppers series has been extensively revised and equipped with new practical features.
For more than 20 years GRIMME has been offering powerful and crop-protecting technology for storing potatoes, carrots, onions and other vegetables and has set the standard with electro-hydraulic drives. For the 2020 season, the RH-receiving hoppers series has been extensively revised and equipped with new practical features.
Perfectly prepared for all transport vehicles
A good seal between the transport vehicle and the receiving hopper minimizes the loss of harvested crop and improves the cleanliness and hygiene of the entire storage process. Since transport vehicles have different contours in practice, the sealing rubber intake flaps must be particularly flexible and quickly adaptable. GRIMME has therefore completely revised the design and function of the receiving area to further improve the quick and safe "docking" of the transport vehicles. The lower support strip, which enables easy rearward manoeuvring to the hopper, especially for transport vehicles with a deep underride guard, is able to move to the rear for improved material protection. Three rubber lips are fitted to the lateral bunker walls, each of them subdivided into three parts. In this way the rubber lips adapt to any vehicle contour. The rubber intake flaps are now ball-bearing mounted. They are height-adjustable without tools, so that it can be quickly and easily adapted to the different heights of transport vehicles. Losses while filling the receiving hopper can now be prevented even more effectively.
VarioFlow: High throughput and crop protection
The transition from the grading or cleaning rollers onto the cross conveyor is often the limiting factor of a receiving hopper, as the crop can only be fed onto the cross conveyor on one side. With the new VarioFlow, GRIMME offers an optional available transfer device consisting of two PU spiral rollers with mechanically adjustable height. With this transfer device, more crop can be transferred more evenly to the crop cross conveyor, which significantly increases the conveying capacity. The transfer height of the two PU spiral rollers onto the cross conveyor can be infinitely adjusted by means of one spindle each on the left and right side of the machine. This adjustment enables the two PU spiral rollers to mesh together when adjusting between different discharge heights, ultimately this leads to increased crop protection. By having a minimum transfer height to the discharging cross conveyor on one side, maximum crop protection is achieved. On the lower side of the conveyor the passage is increased as the rollers are lifted out of the crop flow. At the same time the transfer height remains minimal because the crop is transferred onto other crop on the downstream-side of the conveyor. The result is a significant increase in throughput capacity, while maintaining a high level of crop protection.
Simplified maintenance for the hopper floor drive chain
The new lubricator offers a practical solution for oiling the hopper chain and therefore increases the durability to a maximum. Maintenance and care of the machine is considerably simplified for the operator, as manual lubrication of the hopper floor chain is no longer necessary.
Innovation
Whether its new machines or digital solutions, you'll find all the latest information here.
Display all updates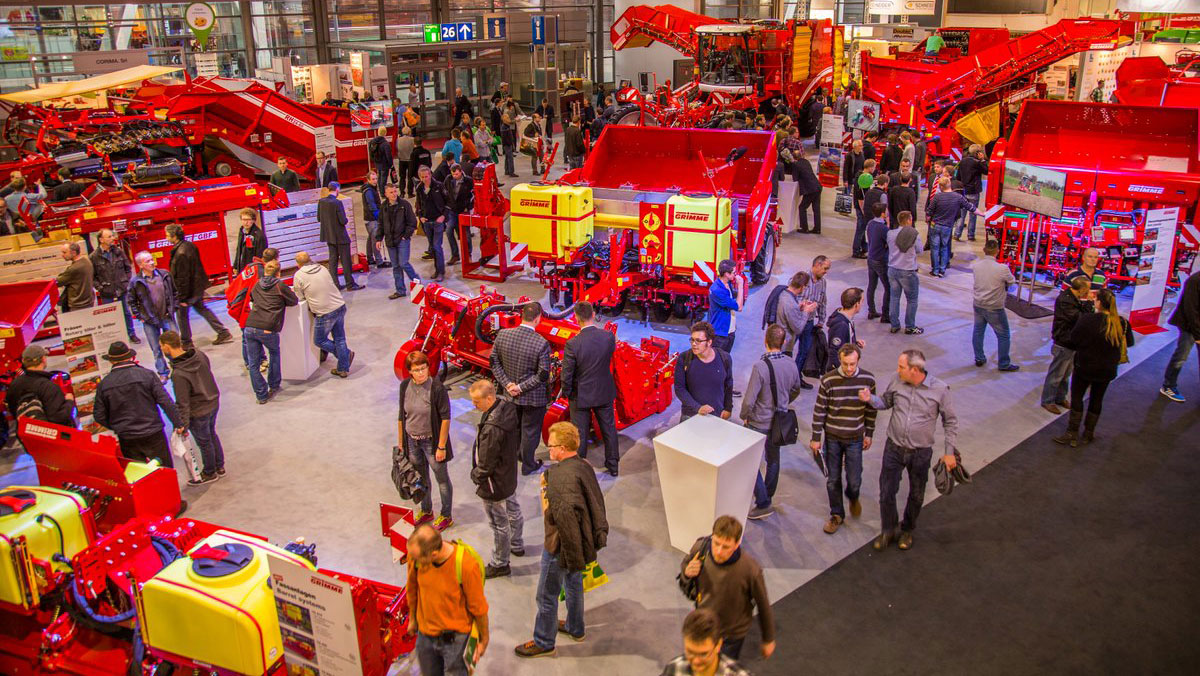